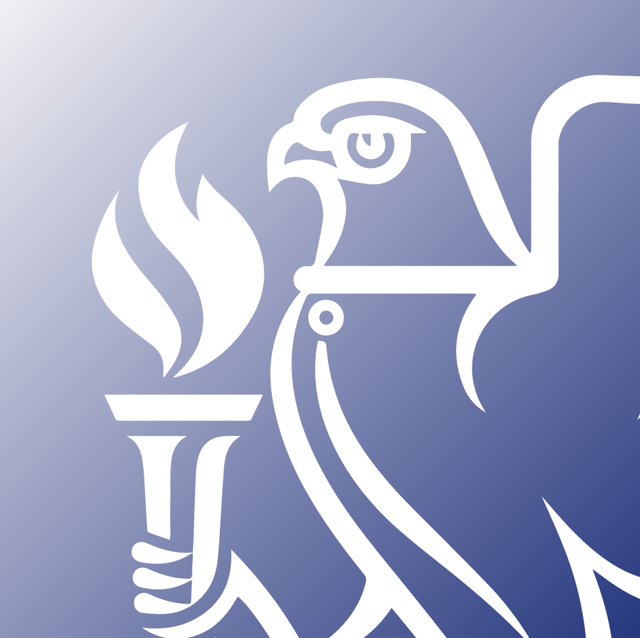
Back to CIBSE Case Studies Overview
Article from the December 2013 edition of the CIBSE Journal written by Graham Smith.
Heat load control is the key to an efficient multiple boiler strategy. Here are the main points to consider.
Traditional temperature-based control strategies are almost universally used for boiler sequence control. However, although limitations have been known for many years, they are often ignored. Here, we look at how strategies based on heat load, rather than temperature, can provide more stable control and effi cient operation.
Most modern boilers, and some older ones, are more effi cient at low loads than at high loads, yet most traditional sequence control systems modulate one boiler up to full output, followed by the next boiler, and so on. Improvement in efficiency at lower loads varies depending on the boiler, but is typically around 3%.
Condensing boilers are more effi cient, with low return water temperatures, but unless the return water temperature is below 54° C, they do not work in condensing mode.
Maximum condensing operation does not occur until return temperatures are as low as 30° C, which can further increase efficiency by up to 8%. However, the mean temperatures necessary for most heat emitters normally preclude return temperatures that are quite so low.
Burner selection
Boilers with modulating burners are common from domestic boilers upwards, and provide more effi cient and stable operation at part load. However, single and two-stage burners are frequently used on larger boilers for reasons of cost.
In my view, modulating burners should be used whenever possible.
Effective sequence control of boilers with single and two-stage burners is difficult and most two-stage (high/low) burners never work in two stages. However, heat load control can enable effective two-stage operation.
Demand-based control/boiler inhibit
Demand-based control systems and boiler inhibit have been available in various forms for many years. Secondary circuits should preferably only be run according to demand, although this can be less practical with larger systems where response needs to be considered.
The lead boiler and pump should be enabled according to demand from the secondary circuits (inhibited when there is no demand). With many systems, the lead boiler can be started when there is a hot water system (HWS) demand, and/ or when the compensated valve is open to heating. Minimum run times need to be incorporated for stable operation.
Dry cycle controllers
Controllers that inhibit the boiler to minimise "dry cycling" (the boiler starting and stopping to maintain temperature during no load conditions) are normally based on flow and return temperature differentials and time delays.
Dry cycle controllers have been found to interfere with boiler purge cycles, creating potentially explosive conditions, inhibiting effective boiler sequence control and reducing boiler modulation at low loads, thus reducing rather than enhancing boiler efficiency.
These controllers are relatively expensive and, in my view, demand-based control strategies are far safer, more effective and better value.
Variable-flow primary and secondary circuits
Modern boilers normally have individual pumps and are connected in parallel via a common header to secondary circuits. This creates variable flow in the primary circuit and increases temperature differential when not all boilers are running.
It is essential that the secondary circuit is also variable flow to prevent dilution of the secondary circuit temperature when all boilers are not on line.
This is often effectively achieved by creating a variable draw from the header via compensated circuit mixing valves, although alternative measures may be necessary with other systems.
HWS segregation
This offers many advantages in most buildings.
Condensing boilers can be operated at lower temperatures, or directly compensated more easily where HWS is independent of heating. Pumping and standing losses are also reduced where heating boilers are shut down in summer.
HWS can be supplied by point-of-use water heaters, or by condensing gas-fired instantaneous/semi-storage units where demands are greater.
Traditional boiler sequence control systems
Traditional multiple boilers, controlled from the boiler primary circuit flow or return temperature, are often unstable or ineffectively controlled.
Control from return temperature is generally considered to be more stable, but can only be used where the primary flow is constant, as the return temperature is only representative of the load in such circumstances. This is still poorly understood by many system designers.
Flow-temperature sequence control can be effective with boilers that have modulating burners and individual pumps. Many modern boilers have a 0-10V control function, which permits either direct modulating control of the burners, or setpoint reset for direct compensation of the boiler. Where direct modulating control of the burner is used, the individual boiler controls should comply with BS EN 15502-1: 2012 for gas-fired boilers, and should limit the maximum outlet temperature via burner modulation to a safe margin below the high limit temperature, regardless of the 0-10V signal. Many packaged boiler controls use PID control loops that are pre-set to provide the most consistent burner modulation under all load conditions. Flow-temperature sequence control must allow for pumps/boilers being started and stopped, with stable control requiring careful commissioning. It is also possible to set up the output stages of flow temperature sequence control to provide more efficient operation.
However, poor commissioning of flow temperature sequence control is common, and frequently ends up with all boilers operating continuously. An increase in proportional band and integral action time rapidly provides stable operation, but this might never be noticed without appropriate witnessing of commissioning.
Flow-temperature sequence control setpoints should be slightly lower than the boiler setpoint (or compensated) to avoid interaction between the sequence control and the boiler controls.
Heat load control
Heat load is calculated from flow and return temperatures and flow rate (Q=MC°t), or via a heat meter which has an analogue heat output in kW. Most modern building management systems can calculate Q=MC°t, so heat meters are not necessary, but can be used.
Magnetic flow meters are considered to be the most accurate and to have the greatest turndown. Ultrasonic are more common and normally used, for example, as an inherent part of heat meters for Renewable Heat Incentive (RHI) applications. Magnetic and RHI heat meters are insertion meters, while clamp-on ultrasonic meters are also available.
Clamp-on meters are less accurate than insertion meters, but flexibility to relocate to the correct location can be beneficial.
Generally the minimum straight length of pipe is 10D upstream and 5D downstream. This needs to be of the same ID as the flow meter for insertion meters. Some ultrasonic flow meters ideally require 20D upstream and 10D downstream, but generally have been found to be sufficiently accurate with 10D/5D for heat load control purposes. CJ
Benefits and downsides of heat flow control
Advantages of heat load control include:
- More stable operation of boilers, particularly at low load
- More efficient operation of boilers, as control can be set in accordance with the most economic operation of the boiler, which is normally at low load above minimum fire
- No risk of interaction between temperature settings of boilers and sequence control, which frequently causes ineffective flowtemperature sequence control
- Effective control of high/low fire boilers is possible
- Effective control of combinations of different sizes/types of boiler
- Effective control where boilers do not reach their rated outlet temperatures
- Normally more rapid and effective commissioning
- Boilers are only enabled by the heat load control; therefore the stable firing of the boiler is entirely the boiler supplier's responsibility
- Direct boiler compensation (reset of setpoint via 0-10v signal) can be incorporated, improving condensing operation
- Often the only effective method of control of bivalent systems.
Disadvantages include:
- Additional capital cost, but this is paid back with long-term effective control
- The systems integrators need to understand the principles of operation and take account of the factors that are essential for effective heat load control.
- And the following factors are essential for effective heat load control:
- Flow meters must be correctly located and commissioned
- Matched flow and return temperature sensors are required
- The lead boiler should be enabled according to demand (or optimum start), as there is no load detected on system start-up when flow and return temperatures are equal. The lag, or subsequent, boilers are enabled according to heat load
- The boiler is normally controlled via its packaged controls, with respect to boiler outlet temperature