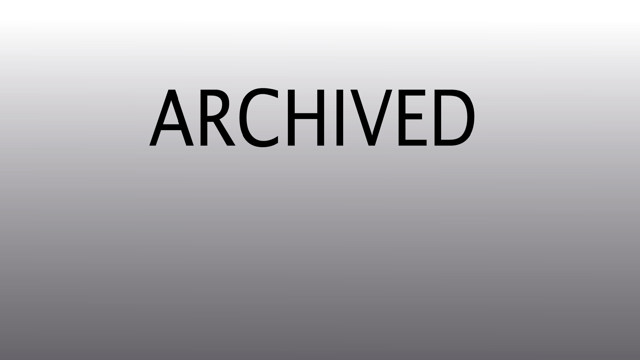
This publication was withdrawn in September 2023 and should not be used on current projects. It is provided here for reference purposes only. The 2023 edition is available here: Guide M Maintenance engineering and management.
PDF only
Table of Contents
1 Introduction
1.1 Scope and structure
2 Guidance for building services designers
2.1 Designer responsibilities
2.2 Advising and guiding the client
2.3 Client requirements
2.4 Installation and maintainability
2.5 Design parameters
2.6 First-year operation and maintenance requirements
Appendix 2.A1: Design guide to maintainable buildings
3 Maintenance strategy and techniques
3.1 Client requirements and other considerations
3.2 Maintenance techniques
3.3 Service delivery options
3.4 Developing and implementing an appropriate strategy
3.5 Selecting the appropriate delivery model
3.6 Implementation and performance management/improvement
4 Maintenance contracts
4.1 Procurement methods and procedures
4.2 Contract selection
4.3 Tender and contract formation
4.4 Documentation
4.5 Contract mobilisation
5 Energy efficiency and maintenance
5.1 Energy strategy and policy
5.2 Energy management systems (EnMS)
5.3 Gaining an overview
5.4 Analysing energy demand
5.5 Legislation and codes of practice in UK
5.6 Investing in energy efficiency
5.7 The energy-efficient brief
5.8 Renewables
5.9 Fuel selection
5.10 Combined heat and power (CHP)
5.11 Metering
5.12 Lighting
5.13 Heating and hot water
5.14 Electrical power
5.15 Controls
5.16 Refrigeration systems
5.17 Justification of energy projects
Appendix 5.A1: Energy benchmark data
6 Controls for building services
6.1 Purpose of controls
6.2 Maintenance requirements
6.3 Building management systems
6.4 Upgrading control systems
6.5 Need for training
7 Commissioning and testing
7.1 Commissioning management
7.2 Summary of commissioning requirements
7.3 Commissioning manager and commissioning specialist responsibilities
7.4 Documentation
7.5 Designer’s checklist
7.6 System characteristics
7.7 Post completion testing
7.8 Continuous commissioning
7.9 Controls and building management systems
7.10 Decommissioning and mothballing
8 Handover procedures
8.1 Preparation
8.2 Sectional completion and beneficial occupation
8.3 Inspections
8.4 User training
8.5 Occupant training
8.6 Tools and spares
8.7 Handover information
8.8 Equipment warranties
8.9 Defects liability
9 Operating and maintenance documentation
9.1 O&M manual content
9.2 Manufacturer literature
9.3 Updating
9.4 Preparation
9.5 Health and safety file
9.6 Building user guides
9.7 BIM information
9.8 Computer-based information systems
9.9 Maintenance management systems
10 Operational risk assessment and management procedures
10.1 Assessing the risks
10.2 Business risks
10.3 O&M risks
10.4 Disposal risks
Appendix 10.A1: Overall risk checklist
Appendix 10.A2: Operational risk checklist
11 Operation and maintenance costs
11.1 O&M cost data
11.2 Cost categories
11.3 Cost data attributes
11.4 Benchmarking
11.5 Levels of information
11.6 Utilisation of labour
11.7 Backlog maintenance
12 Economic life factors and end of economic life
12.1 Background: what are economic factors and when are they used?
12.2 Predicted future life expectancy of assets and components
12.3 Variation factors
12.4 Applications
12.5 Other economic life and financial considerations
Appendix 12.A1: Indicative economic life expectancy
13 Maintenance audits
13.1 Audit document
13.2 Audit details
13.3 Audit scoring system
13.4 Recording comments
13.5 Audit procedure
14 Condition surveys
14.1 Levels and frequency of survey
14.2 Non-intrusive testing
14.3 Consistency of information
14.4 Priority grading
14.5 Condition grading
14.6 Data collection
14.7 Updating information
15 Legislation and compliance
15.1 Legislation
15.2 Requirements for inspection and testing
16 Health and comfort
16.1 Indoor air quality
16.2 Thermal comfort influences
16.3 Air distribution systems
16.4 Comfort during modifications to existing buildings
16.5 Recommended assessment schedules
17 Training
17.1 Management
17.2 Competency
17.3 Training policy statement
17.4 Identification of training needs
17.5 Training plan
17.6 Means of provision
17.7 Certification
17.8 Evaluation
17.9 Records
Principal author: Joanna Harris (BSRIA)
Contributors: Neil Ambler (Watson & Sole); John Armstrong (Armville Consulting); Neil Earnshaw (Constructing Solutions); Rob Farman (Abacus FM Engineering Consultancy); Stephen Gathergood (G4S Integrated Services); Andrew Green (F&G); Paddy Hastings (Norland Managed Services); Steve Hunter (Kaizenge); Paul Kee (Hurley Palmer Flatt); Andrew Martin (Lloyd’s Register); Kate McCormick (SPIE UK); Geoff Prudence; Dave Robinson (Babcock); Andrew Saville (Armville Consulting); David Smith (Datara)
CIBSE Maintenance Task Group and Steering Committee: Neil Ambler (Watson & Sole); John Armstrong (Armville Consulting); Javier Carnero (MITIE); Graeme Craig (B&ES); Neil Earnshaw (Constructing Solutions); Rob Farman (Abacus FM Engineering Consultancy); Steve Gathergood (G4S Integrated Services); Joanna Harris (BSRIA, Chair); Paddy Hastings (Norland Managed Services); Steve Hunter (Kaizenge); Paul Kee (Hurley Palmer Flatt); Gareth Keller (B&ES); Andrew Martin (Lloyd’s Register); Kate McCormick (SPIE UK); Geoff Prudence; Dave Robinson (Babcock); Andrew Saville (Armville Consulting); David Smith (Datara)
CIBSE Referees: John Armstrong; Mike Malina; Phil Taylor