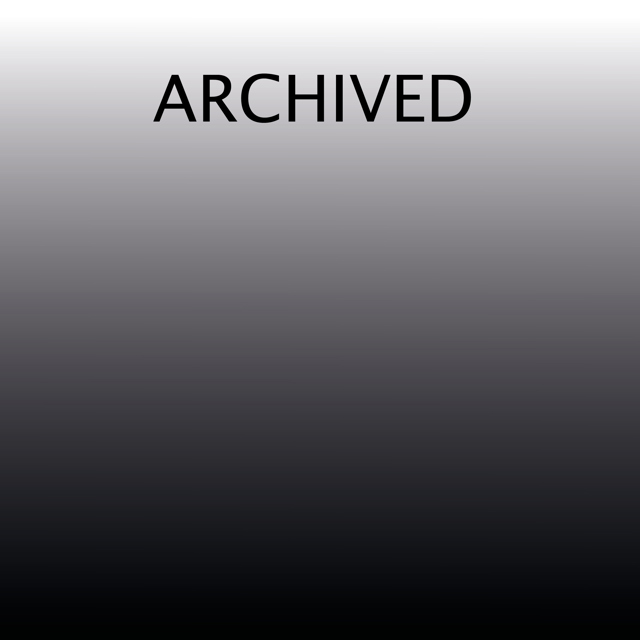
This publication was superseded by Guide M: Maintenance engineering and management in 2008, and again in 2014. The 2008 edition of Guide M is available here, and the current edition is available here: Guide M: Maintenance engineering and management (2014)
Contents of the Guide to ownership, operation and maintenance of building services:
1 Introduction
1.1 Scope and structure
2 Guidance for building services designers
2.1 Designers’ responsibilities
2.2 Advising and guiding the client
2.3 Clients’ requirements
2.4 Installation
2.5 Design parameters
2.6 First-year operation and maintenance requirements
2.7 CDM Regulations
Appendix 2.A1: Design guide to maintainable buildings
3 Types of maintenance techniques and their applications
3.1 Management of maintenance
3.2 Options
3.3 Types of maintenance
3.4 Establishing a maintenance policy
3.5 Choice of maintenance strategy
3.6 Main principles of a planned maintenance system
3.7 Typical range of maintenance services
4 Maintenance contracts
4.1 Contract details
4.2 Components of contract documents
4.3 Types of contract
4.4 Tender and award of maintenance contracts
4.5 Practical difficulties
4.6 Contract management
5 Maintenance strategy and control
5.1 Maintenance strategy
5.2 Control of maintenance
5.3 Operating oversized plant
6 Energy efficiency and maintenance
6.1 Energy efficiency options
6.2 Justification of proposals
6.3 Further guidance 6-3
7 Plant service frequencies
7.1 Statutory service frequencies
7.2 Manufacturer recommendations
7.3 Typical service frequencies
7.4 ‘Standard’ service frequencies
7.5 Inviting tenders
7.6 Adjustment of service frequencies
Appendix 7.A1: Statutory regulations affecting plant service arrangements
8 Heating, ventilating and air conditioning controls
8.1 Purpose of controls
8.2 Maintenance requirements
8.3 Routine maintenance checks
8.4 Building management systems
8.5 Upgrading control systems
8.6 Need for training
9 Commissioning and testing
9.1 Documentation
9.2 Designer’s checklist
9.3 System characteristics
9.4 Fine tuning
9.5 Repeat testing and commissioning
9.6 Controls and building management systems
9.7 Decommissioning and mothballing
10 Handover procedures
10.1 Preparation
10.2 Commissioning
10.3 Inspections
10.4 User training
10.5 Tools, spares and keys
10.6 Handover information
10.7 Equipment warranties
10.8 Sectional completion and beneficial occupation
10.9 Defects liability
11 Operation and maintenance manuals
11.1 Content
11.2 Manufacturers’ literature
11.3 Computer-based information systems
11.4 Maintenance management systems
11.5 Updating
11.6 Preparation
12 Risk assessment procedures
12.1 Business risks
12.2 Design and installation risks
12.3 Operation and maintenance risks
12.4 Disposal risks
13 Owning and operating costs
13.1 Cost data
13.2 Bench marking
13.3 Cost data attributes
13.4 Levels of information
13.5 Utilisation of labour
13.6 Backlog of maintenance
13.7 Data priorities
13.8 Cost predictions for new buildings and designs
13.9 Simple accounting techniques
13.10 Life cycle costs
14 Economic life factors
14.1 Background
14.2 Variation factors
14.3 Economic life factor codes and schedules
14.4 Applications
Appendix 14.A1: CIBSE economic life factor codes and schedules
15 Maintenance audits
15.1 Audit document
15.2 Audit details
15.3 Scoring system
15.4 Recording comments
15.5 Audit procedure
Appendix 15.A1: Maintenance audit check for building services
16 Condition surveys
16.1 Type and frequency
16.2 Thermal imaging
16.3 Consistency of information
16.4 Classifying priorities
16.5 Data collection
16.6 Updating information
16.7 Future developments
17 Health and safety
17.1 Indoor air quality
17.2 Thermal comfort influences
17.3 Air distribution systems
17.4 Modifications to existing buildings
17.5 Recommended assessment schedules
18 The Construction (Design and Management) Regulations
18.1 Design risk assessments
18.2 Risk assessment of work routines
18.3 Plant space requirements
18.4 Maintenance contracts
18.5 Handover documentation
18.6 Views of operatives
18.7 Health and Safety File
19 Training
19.1 Management
19.2 Competency
19.3 Training policy statement
19.4 Identification of training needs
19.5 Training plan
19.6 Means of provision
19.7 Environment
19.8 Certification
19.9 Evaluation
19.10 Records
Principal authors and acknowledgements
Section 1: Introduction: J H Armstrong (Ove Arup & Partners)
Section 2: Guidance for building services designers: M Samuel; R J Oughton; G Prudence
Section 3: Types of maintenance techniques and their applications: J H Armstrong (Ove Arup & Partners)
Section 4: Maintenance contracts: J J Rose (Ove Arup & Partners)
Section 5: Maintenance strategy and control: R Nanayakkara (Building Services Research and Information Association); R J Oughton
Section 6: Energy efficiency and maintenance: R J Oughton
Section 7: Plant service frequencies: R J Oughton; Acknowledgement: Safety Assessment Federation
Section 8: Heating, ventilating and air conditioning controls: R J Oughton
Section 9: Commissioning and testing: R Clark (Commtech Group)
Section 10: Handover procedures: T de Saulles (Building Services Research and Information Association)
Section 11: Operation and maintenance manuals: D Howard (Watson & Sole Associates Ltd)
Section 12: Risk assessment procedures: R Jeeves (Imperial College of Science, Technology and Medicine)
Section 13: Owning and operating costs: M H Smith (Building Services Research and Information Association)
Section 14: Economic life factors: P H Day (engineering consultant); Acknowledgements: ABS Consulting; American Society of Heating, Refrigerating and Air-Conditioning Engineers; Building Services Research and Information Association; Caradon Trend; E-Squared Ltd; Heating, Ventilating and Air Conditioning Manufacturers Association (HEVAC); Krammer & Co; Land Securities Properties Ltd; Metropolitan Police Service Property Services Department Surveying and Engineering Division
Section 15: Maintenance audits: J H Armstrong (Ove Arup & Partners)
Section 16: Condition surveys: D R O’Bryan (ASTAM GBC Consultancy)
Section 17: Health and safety: S Higgins (Winton Environmental Services)
Section 18: The Construction (Design and Management) Regulations: R J Oughton
Section 19: Training: I J Kelly (Lorne Stewart plc)