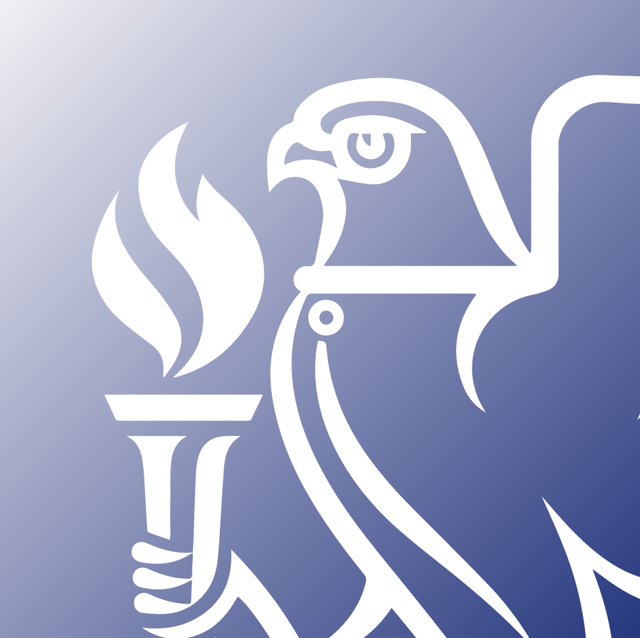
Back to CIBSE Case Studies Overview
Article from the October 2014 edition of the CIBSE Journal written by Andrew Brister.
London's iconic Harrods store won the refurbishment project category at the 2014 CIBSE Building Performance Awards, for a complex 10-year refurbishment that has delivered improved internal conditions, energy reductions, and more resilient building services.
Harrods has come a long way since Charles Henry Harrod established his business in 1824. Today, the brand includes Harrods Bank, Harrods Estates, Harrods Aviation and Air Harrods - but it will always be best known for its iconic store in London's upmarket area of Knightsbridge. Occupying a five-acre (20,000m2) site, and comprising more than 90,000m2 of selling space in 330 outlets - it is the biggest department store in Europe, and attracts visitors from across the globe.
A business that clearly doesn't rest on its laurels, it has ambitious expansion plans for the store, despite the limitations of the site, and the building's Grade II-listed status. "The store continues to expand its retail square footage, while maintaining the existing footprint," a Harrods engineering spokesman points out.
With more shopping space comes higher footfall, and an increasing demand on building services, so Harrods developed an ambitious refurbishment scheme to breathe new life into a store that first opened in the early 1900s. "The rooftop HVAC [heating, ventilation and air conditioning] project is a scheme that started at a conceptual level more than 10 years ago," says the spokesman. The plan was to replace ageing infrastructure, while also introducing additional capacity to support the future expansion plans for the business.
"The ethos was to strive towards reducing energy consumption, improve comfort levels within the store, enhance the resilience of the system, and increase the ability to respond to unplanned plant failure, without impacting other systems," he continues. Retail space has expanded from 925,200 ft2 to 1,381,700 ft2, while the building's annual electricity consumption has decreased from 49,000 MW to 41,500 MW per year. The cumulative effect is a carbon reduction of more than 4,000 tonnes of CO2 each year.
"Considering these reductions have been achieved while increasing the overall footprint of the retail space - where you would normally expect to see an equivalent increase in the electrical consumption - this makes the project more meaningful, and worthy of recognition," says the spokesman. Clearly, the judges at the 2014 CIBSE Building Performance Awards thought so too, because Harrods won the Refurbishment Project (over £5 m) category.
Talking shop
Over the years, Harrods has amalgamated its buildings in Brompton Road, Hans Crescent and Basil Street, and extended upwards. Engineering solutions have slowly evolved around the store, and are now dovetailed into the fabric of the building, making large intrusive refurbishment very difficult. Plant was ageing, inefficient, and under capacity.
Harrods is designed to operate using a full fresh-air ducted system. The fresh air is delivered to the shop floors via large builders' work shafts, which traverse the store from the rooftop down to the basement levels.
The air handling units deliver tempered outside air into the shafts, which are then controlled at each floor level using variable volume dampers. The variable air volume (VAV) system acts according to room temperature sensors by modulating the supply air volume to control the space consisting of multiple air handling units set up in clusters. The units were served by air-cooled chillers positioned close to each cluster, with heating provided from steam coils fed from the basement boiler room. The air handling units' fan speed was varied to maintain the shaft pressures for the VAV system feeding the various dampers. The ductwork system is extensive, and distributes throughout the store, and has become part of the fabric of the building.
While this is an effective means to condition the store, the continual expansion had challenged the system to the point where numerous operational problems were being experienced, admits Harrods. Plant was regularly failing, and was difficult to repair because equipment was often no longer supported by the original manufacturers.
There were problems on the electrical side, too. The store's electrical intake is rated at 11 MW. This was regularly being exceeded and putting a strain on the electrical infrastructure.
The demands of the retailers for more lighting, power and cooling were limited by the maximum intake capacity. Systems regularly struggled to meet the demands of the store retailers, who continually sought higher lighting levels and more extensive display-lighting schemes. Because of the scale of the store, and the extent of the problems experienced, the solution could not simply be found in localised short-term fixes. "Harrods recognised that a more holistic approach needed to be adopted to address the problems, and secure the long-term operation of the store," says the spokesman. "A complete overhaul of the HVAC system was required to address the internal conditions, reduce the store's energy consumption, and increase the system's cooling capacity. It was also imperative to introduce resilience, to mitigate downtime for plant maintenance or failure."
The answer was to deliver a completely new infrastructure, but how to achieve that in a landmark, listed building, while ensuring there was no downtime to the business or disruption to the store's operation? Enter the project team of building services engineer PSK Design, architect Woods Hardwick, structural engineer WSP, and project manager, Riley Consulting.
Delivering the goods
Because of the magnitude of the undertaking, and the budgets involved, it was necessary to deliver the new infrastructure in phases. The design would need to reflect this, without compromising the final solution.
The project team has increased AHU plant capacity by 30% by opting for a compact air handling unit that sits within the same footprint as the existing units.
The units' volumes were increased, yet, by incorporating only one heating coil, one cooling coil and filler bank, the overall energy consumption of the air units has been reduced. All the motors were selected to operate with variable speed drives to align with the pressure control regime, while reducing power consumption.
The specific fan power for each system was reduced from 3.0W/(l/s) to 1.6W/(l/s), while air volumes have increased from 500m3/s to 670m3/s. When in cooling mode, shaft temperatures have been reduced from 16oC to 13oC to increase cooling capacity to the shop floors. Considering the increase in volume and the decrease in supply temperature, the store's sensible cooling capacity has gone up from 4,500kW to 7,900kW, a 75% increase.
Energy-efficient lighting has been introduced throughout the store, with stringent specifications for new retail shop fit-outs, part of the regular turnover within Harrods. "This policy is continually policed, and has reduced the lighting loads from 5.8MW to 3.1MW," says the spokesman. "This involved the retrofitting of general circulation space lighting, as well as display lighting, to LED technologies, while maintaining the lighting levels and colour temperatures."
To improve the system resilience, and join the many roof zones, a 300mm-diameter ring main was installed, where all the chillers and AHUs link together on a primary header, and can be operated as a variable volume system with two-port control. This was required to achieve the energy targets, because analysis of the number of degree days where the building is operating at its balance point showed that the plant would be operating at part loads, and, therefore, lower pump speeds.
This presented a difficult engineering challenge as the operation of a ring main requires central plant with a primary and secondary pumping solution. Traditionally, the chillers would be configured with constant-volume circulating pumps on a primary circuit, to maintain constant flow through the chillers, with variable speed secondary pumps serving the ring main.
The problem with this is that it would require all the plant to be located together, to coordinate primary and secondary sides - which was not possible because of the congestion at roof level.
The use of a primary pumping variable volume (PPVV) system was selected, because the design uses fewer pumps and less piping connections compared with traditional primary-secondary systems, and there is a reduction in the ancillary items, such as electrical supplies, controls and valves. "However, the main benefit is a reduction in the power consumption, and a much-reduced plant footprint," says Harrods. These factors help to reduce the initial cost of the chilled water system, and the small footprint lends itself to sites that have constrained footprints, such as refurbishments. A PPVV design displaces the small, inefficient, low-head primary pumps used in primary-secondary systems. The pressure drops around the central plant, previously satisfied by the primary pumps, are, instead, fulfilled by the main distribution pumps, allowing for the selection of larger, more-efficient pumps, with efficiencies similar to those of the secondary pumps in a primary-secondary system.
There are hurdles to achieving this solution because varying the water flow rate through the chiller evaporator poses a number of challenges, such as: maintaining the chiller flow rate between the minimum and maximum limits of the evaporator to avoid chiller lock out; and managing transient flows without compromising stable operation in multi-chiller plants, to avoid evaporator freezing. By working closely with the design team, chiller manufacturer, control valve manufacturer, and BMS controls installer, the team was able to design out these problems, and deliver a simple, robust and energy-efficient solution, all within a compact footprint.
High coefficient of performance (COP) chillers were required to deliver the increased chilled-water capacities, but reduced overall electrical consumption. To achieve the duties and COP targets, a combination of water-cooled chillers and air-cooled chillers were selected, providing a total capacity of 14.7 MW.
Operationally, this produced performance benefits, because, in the early and late season, there can be wide swings in temperatures. These are best dealt with by dynamic air-cooled machines that can be operational very quickly. The water-cooled machines were configured to provide the base load cooling during the summer months, with the air-cooled machines supporting during the peaks. The COP on the air-cooled machines is 3.7, and 6.2 for the water-cooled.
As part of the refurbishment works, the decision was made to remove the old steam system and introduce low temperature hot water (LTHW ) via a plate heat exchanger.
This eradicated issues with high losses, leaks and safety, and the system now operates as a weather-compensated system, delivering water between 40oC and 65oC to the AHUs. "The project has demonstrated strong collaborative working between the project team in the delivery of a complex refurbishment spread over a 10-year period," says the Harrods spokesman. "The ability to establish a strong design brief early in the process, maintain the principles through design and construction, and deliver the project with no dilution of the original vision is very rare."
The project was completed without any downtime to the stores' operation, despite the replacement of all air handling plant and chillers during some of the coldest, wettest and warmest weather in recent history. The difficulties of working in an iconic Grade II-listed building was never used as an excuse to avoid striving for the best technical solutions. The refurbishment has ensured that there are a few more years in this venerable old store yet.
Existing problems
Issues with the old plant included:
- Existing air handling units were designed to deliver a lowest temperature of 16 degrees C, which limited the opportunity for treating higher-density cooling loads. Hotspots were appearing in Harrods, where central plant capacity was unable to deal with conditions in the store
- The cluster concept meant, when central air handling or chilled water plant failed, there was no ability to back up from other areas or share chilled water from adjacent zones
- Existing plant struggled to respond to seasonal variations in external temperatures. Typically, spring and autumn days, which started cool and warmed quickly during the day, challenged the store's plant and internal conditions.