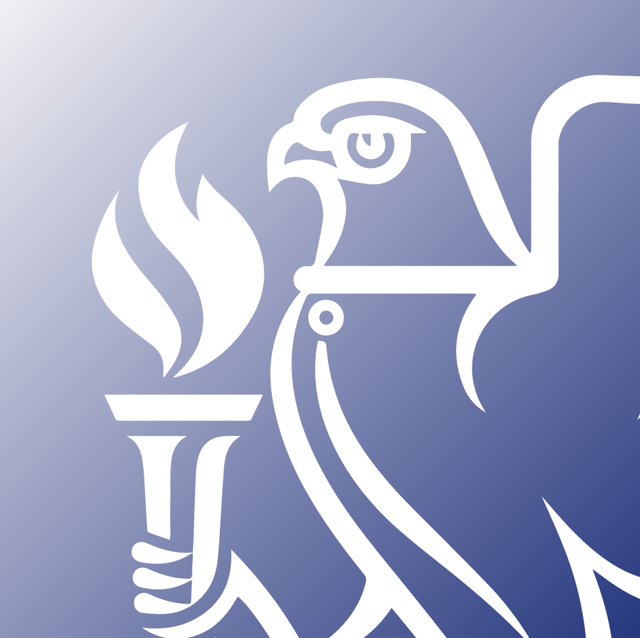
Back to CIBSE Case Studies Overview
Article from the October 2013 edition of the CIBSE Journal written by Keith Bate.
Submarines are among the most hostile environments on Earth, and poorly designed systems can have disastrous consequences. So how do services engineers make these volatile vessels safe to operate and live in?
When I moved from a building services consultancy to work at BAE Systems on the design of Royal Navy submarines, the first question most of my former colleagues asked was, "How does the ventilation work?" often followed by a joke about opening windows. Of course, the services in a nuclear submarine are among the most hard-working on Earth.
The importance of operating the ventilation system correctly, for example, was highlighted by the Chinese Submarine No 361 disaster in 2003, when the 70-man crew was suffocated after the vessel submerged with the diesel engine running.
Add factors such as the need to keep noise to a minimum in order to avoid detection by possible enemies, and the devastating effect can result from faulty pipework, and it becomes clear that the cost of getting the services wrong could not be higher. In this article, I will show how some of the systems used in buildings are integrated into this unique and potentially volatile environment.
Breathing space
Ventilation is obviously a vital consideration in any submarine. When submerged, the air in the submarine is continuously recirculated using centralised fans with electrostatic precipitators to filter out particulates and aerosols, and chilled-water coils to cool and remove excess moisture. Carbon filters are used to extract odours from the galley and bathrooms. Compartments with high heat gains, such as the engine room, are cooled using large-capacity fan-coil units, referred to as air treatment units.
A diesel-electric submarine has to surface regularly to charge its batteries. Running the diesel generators draws in large quantities of outside air, restoring oxygen levels and diluting gaseous contaminants such as carbon dioxide (CO2). To avoid fully surfacing, air is drawn in through a "short induction mast" - a pipe extending just above the surface when at periscope depth.
Although "periscope depth" is still used to describe being submerged with just the periscope above the water, modern submarines don't actually use direct line of sight periscopes any more - digital imaging is now used .
As a nuclear-powered submarine doesn't need air to generate power, it can remain submerged indefi nitely. To maintain a viable atmosphere without surfacing, nuclear submarines are equipped with air purifi cation systems that control the concentration of oxygen (O2), carbon monoxide (CO), carbon dioxide (CO2) and hydrogen (H2).
CO is produced from hot lubrication oil and cooking, and hydrogen is produced by the batteries. Air is passed through a high temperature burner to oxidise these to CO2 and water respectively. CO is kept below 12ppm and H2 below 2%, well below the lower fl ammability limit of 4%.
The CO2 from the burner and from respiration is removed in a dedicated plant using a chemical absorbent that is regenerated by boiling off the gas. CO2 levels are limited to about 5,000ppm, which is significantly above what would be acceptable in a building but below the level that would have long-term health implications for the crew. However, high CO2 levels create a risk of developmental problems for unborn babies. With the introduction of women to submarine service, a method of reducing CO2 levels to 2,000ppm in an isolated area of the vessel is under development for use if a pregnancy is identified at sea.
O2 is generated by electrolysis of seawater that has been purified using reverse osmosis. The O2 level is maintained below an upper limit of 22% to prevent an increased risk of fires, while the lower limit for respiration is a partial pressure of 137 Torr, equivalent to 18% at atmospheric pressure. Partial pressure is used because the air pressure inside a submarine can vary significantly more than in buildings. While normally maintained close to atmospheric pressure, it can vary by more than 25% above or below this for short periods, depending on the operation of various systems. As well as causing ears to "pop", this affects the lungs' ability to absorb O2. Even at a normal atmospheric concentration of 21%, a drop in pressure of just 20% would create a partial pressure of 126 Torr - in the range where physiological effects can be expected.
The quantity of O2 needed is surprisingly small - just 1.25 l/s for 160 submariners. This is equivalent to 7l/s of outside air, less than 1% of the volume provided for the same number of people in a typical building.
The huge disparity is because buildings are principally ventilated for odour control and CO2 dilution, providing far more O2 than is needed. In submarines, odour control, CO2 removal and O2 production are all dealt with separately.
By opening and shutting dampers, the ventilation system can operate in a number of different "line-ups", including full recirculation, providing air for the diesel generators, purging the atmosphere in different parts of the submarine to clear pollutants, and ventilating using outside air when the boat is in harbour.
Pressure on the piping Nuclear submarines have a huge cooling demand. Although surrounded by relatively cool seawater, the heat gains within the submarine far outweigh the losses through the hull. The nuclear reactor, steam piping, electrical equipment and the submariners themselves all generate heat that must be removed. Water-cooled chillers generate chilled water at about 7° C with the condenser heat rejected to a "fresh water" circuit. Major propulsion equipment is generally cooled directly using the fresh water circuit. Heat from this is transferred to the seawater at about 35° C using shell and tube heat exchangers, which serve two purposes: separating the corrosive seawater from the fresh-water system, and allowing the pressure in the system to be kept to a reasonable level.
Pipes carrying seawater are exposed to the same extreme water pressures that act on the hull. The worst submarine disaster in history, the sinking of the USS Thresher in 1963 with the loss of 129 lives, was caused by a leak from poorly brazed seawater pipework. To prevent such incidents, all seawater pipe fabrication and welding is carried out to rigorous standards, with every weld subjected to non-destructive testing. All penetrations through the pressure hull have two in-line valves, so piping can be isolated.
Seawater is also used for drinking and washing, having been treated using reverse osmosis and stored in tanks. The system pressure is kept at about 3 bar using a compressed air supply to the storage tanks. Although not energy-efficient, this is quieter and takes a lot less space than booster pumps.
Submarines present particular challenges for drainage design. Restricted headroom and long runs make it difficult to achieve reasonable falls. Gravity drainage systems rely on liquid flowing downhill, but a submarine can be up to 30° from vertical in any direction. Vacuum systems can be used to address these problems. Sewage waste is stored in tanks , which are pumped overboard when full; tanks of oily waste are disposed of in port.
Another key factor in emergency situations is the compressed air system. In buildings such as manufacturing facilities and laboratories, these systems typically operate at pressures of 10 bar. The air compressors in a submarine operate at nearly 300 bar. This air is mainly stored in groups of bottles suspended in the ballast tanks between the pressure hull and the outer casing.
There are many day-to-day uses for the air such as pressurising tanks, blowing debris out of seawater valves and pneumatic tools.
But the biggest demand on the system - and the main reason for the exceptionally high pressure - is to blow the ballast tanks. Under normal operation, a submarine is designed to be neutrally buoyant, making significant changes of depth using lift from the hydroplanes to effectively "fly" up and down in the water. In the worst-case scenario of losing all power, the last resort is an emergency blow. Opening the emergency blow valve empties the compressed air bottles into the ballast tanks, forcing the water out and lifting the submarine to the surface.
Compressed air can also be used if there is a leak in the hull. The submarine is divided into sections separated by airtight steel bulkheads. Each section can be pressurised so that if there is a leak the air pressure will hold back the water, giving the crew time to make repairs or return to port.
Weight watchers
In buildings, the weight of the engineering systems only needs to be below the allowance in the structural design, which itself includes a significant margin. In a submarine, weight must be managed much more closely as it is crucial to achieving correct buoyancy. Submarines carry lead weights to ensure they can sink but also to make sure they sit level in the water, with the centre of gravity below the centre of buoyancy. Too much weight at either end of the submarine and it will not sit level in the water. Too much weight on the upper decks and the submarine will not stay upright.
The human factor
One of the fundamental differences between submarines and buildings is the role of the users. Most modern building services are computer-controlled and the users have little idea what goes on behind the scenes to keep them comfortable. In submarines, the use of software is strictly controlled, partly due to the potential for cyber attacks. There is a control system to automate many routine day-to-day activities but, if this fails, the systems can revert to manual control. A submarine operates in the most isolated and hostile environment on Earth and the lives of the crew depends on them understanding not only how the systems work but how to keep them going if they start to fail.
The scope of engineering systems in submarines is far wider than one article can cover. However, with the exception of submarine-specific plant such as the airpurification and propulsion systems, the equipment used would generally be familiar to building services engineers. Although the operating environment, hazards and spatial constraints in a submarine are far more extreme than a typical building, the same basic components can form a vital part of some of the most remarkable engineering products anywhere in the world. CJ
Emergency stations
Fire safety in most buildings is based on making sure occupants can be evacuated safely, with fire-fighting left to the emergency services. A submarine cannot be evacuated and poisonous smoke can spread rapidly in the sealed atmosphere, reducing visibility to near zero. This necessitates a very different approach.
In the event of a fire, all fans are stopped and fire dampers shut to prevent the spread of smoke. Because of the limit on the number people a submarine can carry, most members of the crew have more than one role. Anyone not manning a "watchkeeping" position, such as steering the submarine, is employed either actively fighting the fire or in various other parties, connecting hoses, undertaking M&E and emergency repairs, or dealing with casualties.
Strategically located hose reels and fixed suppression systems, such as water spray and aqueous film forming foam, are fitted. Water mist suppression systems are also used on some submarines.
Shock absorbers
Shock is the rapid acceleration of the submarine caused by underwater explosions. To see the damage shock can cause, look up the YouTube video of HMAS Torrens being sunk by the shock wave from a torpedo. The level of shock equipment must withstand depends on whether it has vibration-isolation mounts or is fixed to the structure. Depending on its importance, equipment is either specified to remain operational after a shock event or just to prevent risk to crew. The minimum shock rating for most equipment is equivalent to being dropped from the back of a lorry. For welded equipment, the potential shock level can be 10 times higher.
The "signature" of a submarine, meanwhile, is the noise it makes in the water. A lot of effort is spent making it as difficult as possible for the enemy to detect or identify the submarine. The signature includes turbulence from the propeller, acoustics, vibration, electrical charge and magnetism. Equipment must meet stringent noise and vibration targets and all significant equipment, piping and ducts are supported using vibration-isolation mounts. used on some submarines.