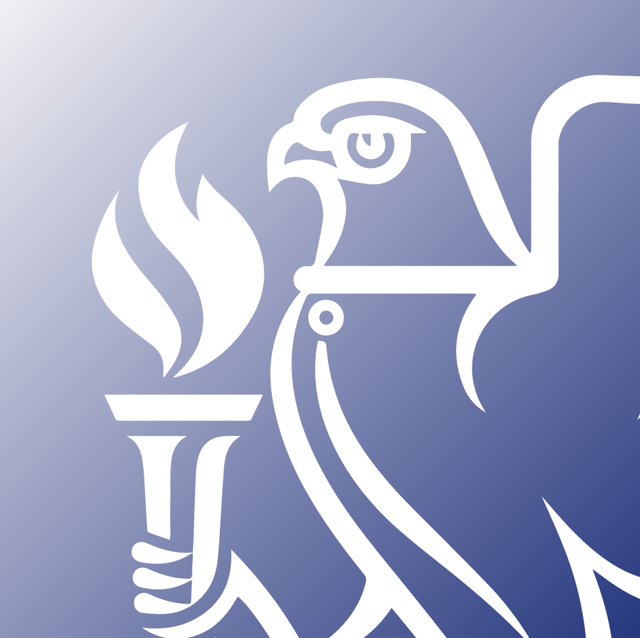
Please note the content of this document can be found below as part of this page. There is no hard copy or download required.
CIBSE Top Tips Information Sheet 2: Lighting in Buildings
This information sheet is intended to help property operators, facilities managers and designers to understand how buildings are lit and what they can do to ensure buildings provide a healthy, comfortable and productive working environment in an energy efficient manner. By following the information provided, building operators, designers and employers will be able to demonstrate compliance with Regulation 8, Lighting, in The Workplace (Health, Safety and Welfare) Regulations 1992. Where there may be concern or areas of high risk then it is recommended that professional advice is sought.
Contents
- Top Tips
- Introduction
- Lighting & health
- How much lighting do I need?
- How the building itself influences lighting
- Daylight
- Design and installation considerations
- Lighting control systems
- Quality of lighting
- Emergency lighting
- Maintenance, examination and testing of lighting
- Cleaning and housekeeping
- The costs and implications of inadequate lighting
- Obtrusive light
- References
- Further reading
Top Tips
- Provide the recommended illuminance on the task
- Ensure the distribution of illuminance on the task is uniform
- Keep the illuminance on the area surrounding the task similar to that on the task
- Avoid confusing shadows in the detail of the task
- Ensure there are no veiling reflections on the task. For work on a computer, this can be achieved by using a high luminance background for the display and a diffusely reflecting screen
- Eliminate disability glare from luminaires or windows
- Reduce discomfort glare from luminaires or windows
- Choose light sources that are free of flicker
- Use occupancy sensors: By dimming or switching off lighting when there is nobody in a room, occupancy sensors can reduce electricity use by 30%
- Use daylight sensors: Adjusting the artificial lighting according to the amount of natural light in a room using daylight sensors or photocells can reduce electricity use by up to 40%
- Have a maintenance plan: By regularly cleaning windows and skylights you can reduce the need for artificial light. Cleaning the fixtures that contain lamps, known as luminaires, will improve their performance
- Emergency escape lighting must be provided and regularly checked.
Introduction
Good quality lighting is lighting that allows you to see what you need to see quickly and easily and does not cause visual discomfort. It does raise the human spirit. The effect of lighting on vision is the most obvious impact of light on humans. With light we can see, without light we cannot. The visual system is an image processing system.
Lighting is vital to the modern world – it enables a 24-hour society to exist. When first introduced, electric lighting was expensive and available to few. Today, it is ubiquitous and cheap. Lighting is used for many different purposes – to ensure visual work can be done accurately, quickly, safely and in comfort; to make places attractive and interesting; to generate business activity; to enhance security and to promote human health. Together these functions make a real contribution to the quality of life of millions.
But lighting comes at a cost, both financial and environmental. The financial cost involves first costs, the cost of the electricity consumed and disposal costs. The environmental cost takes three forms: the consequences of generating the electricity required to power lighting, the chemical pollution upon disposal and the presence of light pollution at night. Lighting is a major user of electrical energy.
The quality of artificial lighting is one of the most important influences on performance in the work place. Some 80% of our sensory input at work comes through our eyes; compromising our vision is, therefore, not an option when considering energy efficiency measures. It is vital to provide good quality lighting that is designed to match the tasks being undertaken and to respect the needs of the occupants. And it is not only the visual effects of lighting that need to be borne in mind; recent research has revealed that lighting has a clear impact on our health and well-being in the work place. The right levels of and the quality of light have been shown to affect alertness and accuracy at work.
Lighting uses some 20% of the electricity generated in the UK and over 75% of lighting installations are thought to be out of date and unable to meet current design standards. The need to reduce carbon emissions presents an opportunity to make lighting more efficient and more effective; so long as the right decisions are made when selecting new lighting.
Lighting and health
Although illuminance on the working plane is the most widely used lighting recommendation, simply providing that illuminance is not enough to ensure good quality lighting. Depending on how the illuminance is delivered, the result can either be comfortable or uncomfortable. Visual discomfort occurs when the lighting makes it difficult to see what needs to be seen, causes distraction or pushes one to the limits of the visual system, all of which are likely to affect visual performance negatively.
Aspects of lighting that can commonly cause visual discomfort are insufficient light, excessive light, shadows, veiling reflections, glare and flicker. Following the illuminance recommendations given in the Society of Light and Lighting (SLL) Code for Lighting (Chapter 2) for various workplaces, will almost always ensure that the extremes of insufficient light and excessive light are avoided.
More details of the situations in which shadows, veiling reflections, various forms of glare and flicker occur can be found in the SLL Lighting Handbook. If in any doubt seek competent advice from a lighting specialist.
Eyestrain
The consequence of prolonged exposure to uncomfortable lighting conditions is likely to be eyestrain. The symptoms of eyestrain vary in form and magnitude from one individual to another but headache, blurred vision, dry or watery eyes, tense muscles and burning or itching eyes are common. Sleep or resting the eyes for a time usually alleviates the condition. While eyestrain can be annoying, it rarely indicates a serious eye problem. Nonetheless, anyone who frequently experiences eyestrain cannot be said to be enjoying the best of health. There are a number of lighting recommendations designed to minimise the occurrence of eyestrain. The illuminance on the working plane and the illuminance uniformity across that plane are intended to ensure that all the tasks likely to occur in the space under consideration will be highly visible. The luminance ratios recommended between the task area, the immediate surround and the background seek to maximise the visual acuity and contrast sensitivity of the visual system and minimise the likelihood of discomfort glare occurring. The ranges of room reflectances have a role to play in increasing the amount of inter-reflected light in a room and hence reducing the magnitude of any veiling reflections.
How much lighting do I need?
Detailed design guidance is available in the SLL Code for Lighting. Specific requirements will be based on the tasks being undertaken. Typical illuminance levels are from 100 – 1000 lux.
How the building itself influences lighting
Aspects of the work environment that need to be considered are:
- level of natural light;
- interior design;
- working conditions.
Level of natural light
Most people prefer to work in natural daylight, therefore it is important to make full use of it. Daylight by itself does not usually provide sufficient illuminance throughout the whole working area or for the entire working day; in most circumstances sufficient and suitable lighting can be provided by a combination of natural and artificial lighting. However, some workplaces have no natural light owing to architectural layout and, in these cases, suitable artificial lighting needs to be present so that work can be done safely and efficiently.
Natural light on its own, or combined with artificial lighting, can be a source of glare and/or reflections. Where it is not possible to adjust the position or location of the display screen or work station, adjusting the illuminance in the workplace may solve the problem. If not, anti-glare screens for VDUs may be used as a last resort.
Interior design
Constraints imposed by the layout of the workplace may result in the employer choosing a particular lighting design. For example, an open-plan office with large windows will have different lighting requirements to small individual offices with few windows.
Furniture and equipment in an open-plan office may cause excessive differences in the illuminance between areas.
Lighting design needs to allow for this, especially in areas where illuminance may be insufficient to carry out a task safely.
The choice of colour in a room is also important because dark surfaces reflect very little light. Light reflected off the walls is usually distributed more evenly than direct lighting. It can soften shadows and will tend to reduce the effects of any veiling reflections and glare. The reflectance of surfaces may be calculated by using a method outlined in BS 4800: Schedule of paint colours for building purposes.
Working conditions
It is important that an employer considers the working conditions in which lighting is used. Conditions which create dusty, flammable or explosive atmospheres may require a lighting design that protects against dust ingress, is robustly constructed and does not ignite. Care must also be taken to keep away any objects (for example curtains and shelves) that may be damaged by lamps that operate at high temperatures (for example tungsten halogen).
Daylight
Daylight is the only freely available light source and yet all too often it is overlooked; well controlled daylight can provide a space with the best possible lighting effect, superb colour rendering, great user comfort and with zero cost or CO2 emissions.
Design and installation considerations
The type of lighting installation chosen depends on:
- its suitability for use;
- whether it is safe for use;
- the size of area to be covered;
- the physical constraints of the space; and
- the purpose for which it will be used.
Interior lighting can be split into three categories:
- General lighting provides uniform illumination over the whole working area and does not limit positioning of the work;
- Localised lighting provides different levels of illumination in different parts of the same working area. It matches the level of illumination to the needs of specific tasks;
- Local lighting is usually a combination of background lighting and a luminaire close to the actual work area. It is used when: (a) a high level of illumination is needed in a small area; (b) flexible directional lighting is required, for example when doing different tasks at a workstation; (c) general lighting is unnecessary or impossible to install because of the layout of the work area.
Lighting control systems
A control system can be anything from a simple mechanical switch to a sophisticated automatic control system capable of responding to the amount of daylight present, or to area occupancy.
Do not place manually operated switches in a position where employees have to reach past machinery or cross an unlit area to operate them. Similar considerations apply to automatic control systems. Lighting installations with such systems should include a ‘fail safe’ facility so that if the control system fails, no occupied area will be plunged into darkness. Automatic control systems also need to include a manual override which can be used if the automatic system fails.
Quality of lighting
A wide range of lamps is commercially available. Different lamp types produce light in different ways and so have different properties. More detailed information is given in the Lighting Industry Association’s Lamp guide.
The choice of lamp depends on certain factors, such as the type of workplace in which it is to be used, luminous efficiency and service life. Lamps and luminaires must:
- support and protect the light source;
- provide safe electrical connection;
- be safe for installation, use and maintenance;
- where practicable, provide filtering to remove harmful levels of radiation.
Guidance on luminaire types, their standards and markings is available in SLL Code for Lighting. Each luminaire is designed for a specific lamp or range of lamps. If lamps are put in the wrong luminaires this may result in glare and decrease the life and operating efficiency of the lamp. Using luminaires in situations for which they are not designed (for example, low-pressure sodium lamps in a potentially wet environment) can be dangerous. Expert advice is available in SLL Lighting Guides 1 to 9 for various workplaces.
Emergency lighting
Emergency lighting is a legal requirement in almost all premises. Details of emergency lighting systems can be found in SLL Lighting Guide 12: Emergency lighting (2022).
When the normal mains lighting fails in areas without natural light, it is necessary to evacuate the premises, to move people to a place of safety or to allow essential processes to continue or be shutdown. During this period, emergency lighting should be provided from a source independent of that supplying the normal lighting.
Emergency lighting can take several different forms depending on its purpose. The first division is between escape lighting and standby lighting. Escape lighting is designed to ensure the safe evacuation of the space. Standby lighting is designed to enable continued operation of space. Escape lighting is subdivided into the lighting of the escape route, the lighting of open areas where there is no defined escape route and high risk areas where a hazardous activity takes place and needs to be made safe before evacuation.
Emergency lighting should be considered as an integrated part of the building lighting. Unless this is done, there is a risk that the normal lighting and the emergency lighting will clash in appearance to the detriment of the whole scheme.
Emergency lighting can be provided using either self-contained units or a centrally powered system using either batteries or a motor-generator set. A self-contained unit contains its own power source and can be a stand-alone luminaire or an emergency version of the normal lighting luminaires. Central systems provide power to the emergency light source via separate, protected wiring to slave luminaires.
The running costs of central systems are usually lower than those of a system using self-contained luminaires, as only the central unit needs to be monitored whereas self-contained units need regular servicing and replacement of the battery packs.
Maintenance, examination and testing of lighting
Lighting systems need to be kept in effective working order. Maintain the systems as advised by the supplier or installer. In the absence of such information, guidance is available in B&ES SFG 20. CIBSE Guide M Maintenance engineering and management provides good practice information. Follow any special safety procedures before any systems are accessed. Do not forget you may need PPE for some maintenance tasks.
Inspection of a lighting installation system will usually start with a visual check of all the equipment (e.g. luminaires, switching, controls and control settings, wiring). Such inspection should be at least once a month for signs of damage or faults.
Cleaning and housekeeping
By regularly cleaning windows and skylights you can reduce the need for artificial light. Cleaning the fixtures that contain lamps, known as luminaires, will improve their performance.
The costs and implications of inadequate lighting
Poor lighting can not only affect the health of people at work causing symptoms like eyestrain, migraine and headaches, but it is also linked to Sick Building Syndrome in new and refurbished buildings. Symptoms of this include headaches, lethargy, irritability and poor concentration.
Poor lighting at work can represent a significant cost to business in the form of:
- time off work as a result of accidents and injuries;
- increased absenteeism;
- reduced staff efficiency and productivity.
Obtrusive light
Outdoor lighting can make a valuable contribution to people’s work, safety and enjoyment after dark, but it can also be obtrusive. This is not inevitable, but it is possible and depends on how the lighting is designed and used. Obtrusive lighting can be said to be occurring when people complain about sky glow, light trespass or glare. Obtrusive light has the potential to be a problem in both new and existing lighting installations (see SLL Guide to Limiting Obtrusive Light).
References
B&ES (2012) B&ES SFG 20 Standard Maintenance Specification for Building Services (Penrith: B&ES)
BSI (2011) BS 4800: 2011 Schedule of Paint Colours for Building Purposes (London: British Standards Institution)
CIBSE (2014) Guide M Maintenance Engineering and Management (London: Chartered Institution of Building Services Engineers)
Lighting Industry Association (2009) Lamp Guide (On-line - see http://www.thelia.org.uk/lighting-guides/lamp-guide)
SLL (2012) Code for Lighting (London: Society of Light and Lighting)
SLL (2009) Lighting Handbook (London: Society of Light and Lighting)
SLL (2012) Lighting Guide LG1 The Industrial Environment (London: Society of Light and Lighting)
SLL (2008) Lighting Guide LG2 Hospitals and Health Care Buildings (London: Society of Light and Lighting)
SLL (2006/2013) Lighting Guide LG4 Sports Lighting (with 2013 Addendum) (London: Society of Light and Lighting)
SLL (2011) Lighting Guide LG5 Lighting for Education (London: Society of Light and Lighting)
SLL (1992) Lighting Guide LG6 The Outdoor Environment (London: Society of Light and Lighting)
SLL (2005) Lighting Guide LG7 Office Lighting (London: Society of Light and Lighting)
SLL (2014) Lighting Guide LG8 Lighting for Museums and Art Galleries (London: Society of Light and Lighting)
SLL (2013) Lighting Guide LG9 Lighting for Communal Residential Buildings (London: Society of Light and Lighting)
SLL (2015) Lighting Guide 12 Emergency Lighting Design Guide (London: Society of Light and Lighting)
SLL (2012) Guide to Limiting Obtrusive Light (London: Society of Light and Lighting)
TSO (1992) Workplace (Health, Safety and Welfare) Regulations 1992 No. 3004 (London: TSO)
Further reading
BSI (2011) BS EN 12464-1: 2011 Light and Lighting – Lighting of Workplaces – Part 1: Indoor Work Places (London: British Standards Institution)
BSI (2014) BS EN 12464-2: 2014 Light and Lighting – Lighting of Workplaces – Part 2: Outdoor Work Places (London: British Standards Institution)
Carbon Trust (2011) Lighting Overview Guide (CTV049) (London: Carbon Trust) See http://www.carbontrust.com/resources/guides/energy-efficiency/lighting (which includes links to other free CT lighting publications)
CIBSE (1999) Technical Memorandum TM24 Environmental Factors Affecting Office Worker Performance: A Review of Evidence (London: Chartered Institution of Building Services Engineers), See http://www.cibse.org/knowledge/cibse-tm/tm24-environmental-factors-affecting-office-worker
HSE (1998) HSG38 Lighting at Work (London: HSE Books) See http://www.hse.gov.uk/pubns/books/hsg38.htm
HSE (2013) L24 Workplace (Health, Safety and Welfare) Regulations 1992. Approved Code of Practice and guidance (London: HSE Books) See http://www.hse.gov.uk/pubns/priced/l24.pdf
TSO (1992) Workplace (Health, Safety and Welfare) Regulations 1992 No. 3004 (London: TSO)
© CIBSE 2015